Do you need Voltage Reduction Device for your Welding Machine?
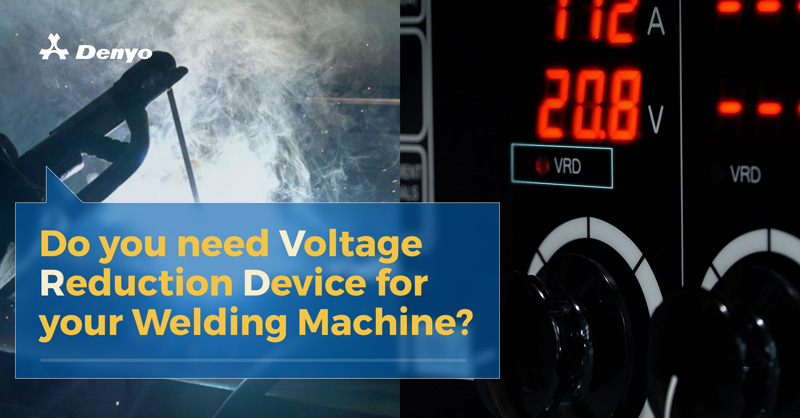
We cannot emphasise enough on the importance of welding safety as it should be fundamental for any projects – if ignored, one would risk facing an array of life-threatening hazards. Electric shock being one of the most dangerous and immediate risks facing a welder – there is one single device you ought to know – for it could be a life-saver against electrocutions. And that is the Voltage Reduction Device, or more commonly known as VRD. That said, let us discuss why VRD could be the next safety enhancement you will need.
Electrically Hazardous Environments
A weld that could be readily performed in a controlled space becomes more complex when sited in confined space and high humidity environments. Also, unfavourable conditions often put welders at risk, with an increased likelihood of electrocution.
A secondary electric shock can occur when a welder accidentally touches the electrode and welding work. Therefore, welding in a confined space often leaves the welder in cramped positions, posing a huge risk of accidental contact with conductive parts.
In most cases, welders would wear dry gloves, avoid touching the electrode with skin or wet clothing and keeping dry insulation between their body and the metal being welded or ground. But when welding in wet, damp or humid conditions, it reduces the skin resistance of the body and insulating properties of standard PPE (Personal Protective Equipment), which increases the risk of getting an electric shock!
Hazard-Reducing Technology, VRD
Fig. 1 Operation of the electric shock prevention function (typical example)
Along with the conventional safety practices, do you know that a VRD is designed to reduce the voltage present to a safer level? Fig. 1 shows a typical example of a VRD operation. The output terminal voltage is about 13V during non-welding periods. When welding starts, the output terminal voltage will be the load voltage (arc voltage + voltage drop due to cable voltage drop).
When the welding rod is removed from the base metal, and the arc turned off after welding is complete, the terminal voltage will be the no-load voltage (60 to 80VDC), which will be reduced by the VRD to about 13V within a second. Thus, the VRD will cause a slight decrease in arc start performance. The high no-load voltage occurs only momentarily at the start of an arc. Therefore, should the output terminal, the welding holder, or the electrode section of the welding rod come into contact with the skin, the risk of getting electrocuted from the secondary electric shock has been reduced.
Safety awareness has risen among users; many countries have introduced statutory requirement to equip welding machines with VRD function. In our proactive adoption of safety measures, Denyo have developed welding machines equipped with VRD function as a standard. So If you have any questions or upcoming projects that may require the use of VRD technology, do not hesitate to contact us for a non-obligatory discussion to address your concerns