How to Choose an Air Compressor?
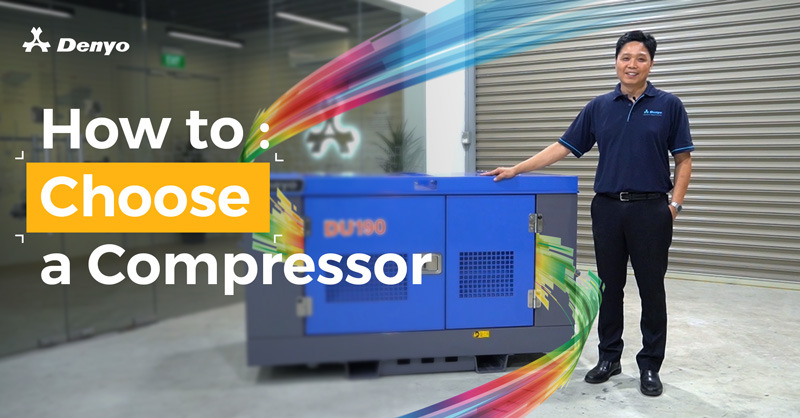
Air compressors are versatile machines and perform a variety of tasks when attached to pneumatic tools. They produce more torque and power and last longer compared to electric power tools. They have many applications, types and capacities, which can be confusing if you are not familiar with compressors.
Through this article, we want you to be able to clearly understand air compressor before making any decisions. So, let us explore the five decisive factors of air compressor – that best suits your applications.
1. Air Compressor Grades
Consumer-grade air compressor is mainly for low pressure – single tool usage. Most commonly found in household or small garage workshop.
Contractor-grade air compressor is portable yet capable of providing a steady supply of compressed air. Typically wheeled, or mounted on a small vehicle to enable use of pneumatic tools on work-sites.
Commercial air compressor is continuous high pressure, heavy-duty air compressors that can power multiple tools at a time. Designed to be fixed in one place, they are most suitable for industrial and marine usage.
2. Type of Compressor: Single or Two Stage?
A Single-stage air compressor is typically smaller in frame size and has a lower amount of pressure – for the compression process only happened once.
Whereas for Two-stage air compressor, the compression process happened twice to double the pressure. While a two-stage compressor produces higher air power, they often cost more and produces more noise.
3. Air Pressure and Delivery of the Air Compressor
Your air compressor’s specifications will mainly depend on these 3 factors:
CFM, or Cubic Feet per Minute, is the air compressor’s flow rate, or the amount of air that an air compressor can produce at a given pressure level.
In data points, 1 (cubic meter / minute) = 35.32 CFM.
PSI, or Pounds per Square Inch, is the amount of force that an air compressor can deliver.
In data points, the bar is a metric unit of pressure and 1 bar is equal to 14.5 PSI.
HP, or Horsepower, is the amount of power that an air compressor’s motor or engine can produce.
In data points, kilowatt is a unit of power and 1 kilowatt is equal to 1.34 HP.
4. Rotary Screw or Piston Air Compressor?
Piston air compressor is the most common type of compressor, and they work on the basis of valves and piston rings. They are relatively inexpensive, but are louder and supply a lower air output delivery, as well as lower air quality.
Rotary screw air compressor works based on two intermeshing rotating screws and is generally more expensive. They offer a steady flow of air – without pulses and fluctuating pressure that can be associated with a piston air compressor.
5. Power source of the Air Compressor
Choosing between an Electric motor or Diesel engine to power an air compressor has always been a topic that sparks off considerable debate.
While diesel engines have increased in prices over the years, their technology and performance have also improved dramatically. Even though an electric-powered equivalent is generally quieter and emission-free – to a certain degree. All these advantages are irrelevant if a power supply isn’t available on-site, and this suggests that a diesel-driven option is a more versatile solution for work sites in remote locations.
Work with a Reliable Partner
In this article, we have identified 5 decisive factors of air compressor to help you choose the one that best suits your application. Lastly, your air compressor has to be reliable, coupled with excellent local support to keep it at optimal condition through its service life.
If you have any further questions, we welcome you to contact us for a non-obligatory discussion. Also, keep up with Denyo news and stories for more workplace safety tips, latest machinery technologies and recent happenings.